
All SAILOMAT operations are closed. This website is presented for historical reasons. Happy sailing!
QUESTIONS AND ANSWERS
Answers given by SAILOMAT designer Stellan Knöös
- Which is the best self-steering principle?
- How does the servo-pendulum windvane system operate?
- Why is the SAILOMAT self-steering superior to other systems?
- How is SAILOMAT a safe system against blade and shaft breakage?
- Your comments on the design philosophy of using alloy aluminum plates and extrusions?
- What about corrosion?
- Why is welding not used for the SAILOMAT?
- Why is SAILOMAT simpler to install?
- Can the SAILOMAT be mounted off-center, and what are the disadvantages, if any?
- Why is the SAILOMAT oar blade slanted 34 deg back- while competitor systems have a vertical blade?
- What about overload safety?
- Can the SAILOMAT be operated with a small electrical autopilot as signal input, instead of the air vane?
- Can the SAILOMAT be used for self-steering while motoring?
- When to select an optional Remote Course Control (RCC)?
- Do the SAILOMAT bearings need lubrication?
- Do we need a spare parts kit?
- We have a ketch with low mizzen boom that extends aft of the transom. Can we use a SAILOMAT?
- We have hydraulic steering. Can we use the SAILOMAT?
- Do we need to reinforce the transom when mounting the Base Plate of SAILOMAT 700?
- How simple is it to install a SAILOMAT?
Definitely the so called servo-pendulum principle with a servo (oar) blade suspended in a pendulum carriage, a near-horizontal pivot air vane, and pull lines to tiller or wheel.
This principle offers both high steering torque and desirable yaw damping. The SAILOMAT is built on this principle.
Other principles, such as a vane controlling a trim tab or an auxiliary rudder, usually result in poor steering torque and unacceptable (yaw) damping characteristics, and should therefore not be seriously considered.
Sailing the correct course, the vane base is initially turned to orient the (air) vane surface to be parallel to the wind (air vane is vertical). If the yacht is falling off course, the corresponding aerodynamic force will slightly tilt the vane, and the vane-to-oar linkage to turn the oar blade.
Waterflow 'side-lift' drives the oar pendulum slightly to the side ('swing' motion), pulling the pull/pull lines to the tiller or the wheel, and the main rudder to accomplish the steering course correction.
The pendulum swing should be proportional to the initial course deviation. This action is usually fast, highly accurate and, if designed correctly, also properly damped to avoid course oscillations (yawing).
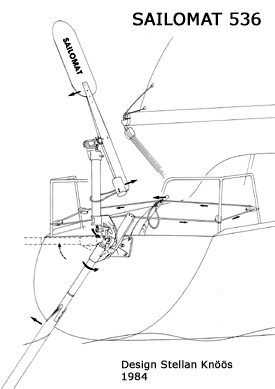
Why is the SAILOMAT self-steering superior to other systems?
Basically because it is better designed, with a much higher 'performance parameter' = steering torque per degree course deviation. But also due to the unique (patented) engineering design that goes into it, with several superior features just not available with the competitor systems.
The patented SAILOMAT design is state-of-the-art and highly efficient. The individual components are strong and simple, and linkages designed for durability and minimum friction. The many design parameters such as sizing of the air vane and oar blade surfaces, oar blade turning angles, variable vane-to-oar ratio , pendulum and 'tow in' stability features are all carefully optimized after years of experimentation and engineering analysis. The hardware is particularly simple and robust, requirements for high reliability and durability.
The strength-to-weight ratio is also optimized, assuring best possible overall performance and function. The SAILOMAT strength-to-weight ratio is currently 2.5 to 3 times better than stainless steel competitor gears. The strength of the most important and 'critical' lower section of the oar shaft is over 400% (!) higher than most competition, primarily due to the superior overall design and choice of light alloy materials for the SAILOMAT.
The SAILOMAT also comes with a vane-to-oar variable ratio, a patented exclusive SAILOMAT feature, with ability of system sensitivity tuning and better performance in light winds. The variable ratio feature offers a substantial beneficial gain in steering torque (line output) over a conventional fixed ratio.
In my opinion many of the current competitor self-steering systems and systems of the past are all built too weak for demanding blue water cruising. This is particularly true for stainless steel designs, where the overall weight (and the manufacturing cost) would be unacceptably high if one would first specify and require an appropriate strength. This argument applies to all the individual components that make up the self-steering gear, and valid particularly for the oar shaft and servo blade which are both subject to the high loads.
Reported shaft and blade overload breakage mostly occur at the mechanical limit for the pendulum swing motion, by design limited to only 30/30 deg to each side for the competitor gears, and when the pendulum hits the limiting 'cage' for those systems. The caged (limited swing) pendulum, combined with very thin tube walls for the oar shaft, result in strength and durability problems with these designs.
By contrast, the patented SAILOMAT 700 design permits the pendulum total 'swing' as much as 148 deg to port side and 120 deg to the starboard side. The total SAILOMAT 700 swing ability is then a full 268 deg, compared to only 60 deg for the some competitors. In an emergency situation, a rapid manual turning maneuver under sail or power would slam the competitor blade into the mechanical 30 deg limit with the possibility of fatally overloading it. Instead, the SAILOMAT 700 blade would respond by swinging beyond the 30 deg limit, even out of the water, thus completely avoiding equipment damage.
For even further protection and superior durability, the SAILOMAT shaft/blade assembly is designed to unparalleled strength.
Due to the above high-strength design features used on all modern SAILOMAT pendulum systems first used on model 500/536 from 1984, then again used for models SAILOMAT 600 in 1992, SAILOMAT 601 from 1995 and SAILOMAT 700 from 2005, not a single SAILOMAT pendulum or blade component has yet broken since market introductions, a remarkable and unmatched durability record!
For a high-performance self-steering system you want high strength in combination with lowest possible weight. In that respect aluminum alloys are the most feasible for this demanding marine application and superior to most other metals, including stainless steel (such as ss 303, 304, 316 or 316L). Extruded aluminum alloy 6061-T6 (density 2.8 g/cm3) and other similar alloys are presently used for the SAILOMAT.
Theoretically, the aluminum system weighs only 27% compared to a similar system of stainless steel (ss 316, ss316L, density 7.8 g/cm3) for a design of 'given strength', incorporating the fact that the yield strength (maximum permissible load) for aluminum 6061-T6 is 28 kp/mm2 (40,000 psi), and 33% higher than for 316/316L stainless steel with 21 kp/mm2(30,000 psi). This also means that for the same overall weight a 6061-T6 aluminum design can be built 3.7 times (!) stronger than a corresponding stainless steel system.
With similar overall weights, the current SAILOMAT model has a several hundred
percent strength advantage over the competition stainless steel systems due to
the combination of
1) the selection of the superior light alloy over stainless, and
2) the state-of-the-art SAILOMAT design.
For the very same reasons we build advanced airplanes, and sailboat masts and hulls in light alloy materials and not in stainless steel!
Marine grade light alloys have been used successfully in all SAILOMAT self-steering designs for over 30 years. It also permits the use of advanced manufacturing techniques for compact, clean looking and highly efficient components.
Why is welding not used for the SAILOMAT?
In using light alloy aluminum material for the ocean environment one would have to address and carefully look at potential corrosion problems involving welding, electrolysis and fasteners.
Welding is completely banned from the SAILOMAT design, thus avoiding the corrosion problems normally associated with welding.
A zinc sacrifice anode is used to minimize galvanic corrosion.
For all stainless steel fasteners we use stainless Nylock nuts, and stainless washers for the current SAILOMAT systems.
Installation simplicity for the SAILOMAT 700 basically comes from our patented 'small-footprint' (200 x 240 mm width/height) base plate concept. Only four attachment bolts are required for the base plate attachment to the transom, compared to as many as 16 (!) bolts for some competitors. Considerable and unique mounting simplicity is achieved with the SAILOMAT 700 Universal Base concept, allowing turning of the main SAILOMAT 700 center plate on the mounted base plate, and thus obtaining the desired position of the SAILOMAT unit (vertical mast tube).
The SAILOMAT is designed to permit off-center mounting. Off-center mounting is of interest if you want to keep a swim ladder or a swim platform in original positions, for yachts with outside hung rudders, or to obtain unobstructed space for a sugar scoop or walk thru transom section.
Off-center mounting of the center plate of the SAILOMAT 700 up to 300-350 mm is possible with insignificant performance reduction.
We designed the SAILOMAT pendulum systems with considerable slant angle for several important reasons. One reason being the superior ability for a heavily slanted blade to rid itself and 'pump off' any sea weed that may wrap around the blade and reduce performance. Other reasons relate to 'toe-in stability' and important yaw damping. The chosen SAILOMAT slant angle also permits convenient and clean installations to modern hull configurations, e.g. with sugar scoops and walk-thru transoms.
Forward impact protection of the servo blade is guaranteed by a plastic sheer pin.
Yes. The input signal to the SAILOMAT system is then magnetic course rather than wind vector. We recommend to use a small linear-motion 'cockpit autopilot', with the attachment for the (linear) actuator arm connected the SAILOMAT counterweight or vane rod. The autopilot base could be secured to the pulpit. Scheme benefits include significantly smaller electric power drain (= idle load), much less frequent battery chargings, and significantly increased autopilot life and durability.
Autopilot control, instead of the normal air vane, could be used when sailing in areas e.g. with many islands and disturbing directional wind shifts, narrow channels, when motoring, and when motoring in dead true or apparent wind.
Only at lower hull speeds and for limited periods of time. However, it is important that the servo blade is positioned -which is possible with SAILOMAT 700- outside any turbulent propeller slip stream to avoid damaging vibrations to the system. Adjusting the 'neutral' position of the SAILOMAT blade to be outside the slip stream is done by lengthening or shortening of the vane-to-oar pushrod, by turning of the vane base a few turns on the mast tube.
An all-mechanical RCC (coaxial drum on mast tube + control line to the cockpit) should be considered only when you cannot easily reach the standard course control handle. This is normally the case only for larger yachts with center cockpit, and for special situations when the SAILOMAT is mounted in an extreme aft position, e.g. behind an outside hung rudder. For 95% of the applications an RCC is not required or recommended.
Yes, all the SAILOMAT 700 bearings benefit from frequent cleaning of salt deposits and addition of a salt water resistant grease.
For longer passages we recommend to carry replacement bearings, additional air vanes, shear pin and some metric fasteners.
Yes. Please contact our Design Office for a custom design solution that may include special custom-built air vanes.
Normally not. With hydraulic steering it is not possible to connect any servo-pendulum system to a wheel coupling disc on the wheel, since leakage of the hydraulic fluid across the pistons will gradually cause the wheel to turn slowly under helm, for which the line circuit cannot compensate.
However, special arrangements can be made to solve this problem and to still use a SAILOMAT. The solution involve coupling to a direct emergency tiller or quadrant, with a bypass hydraulic valve. Contact the SAILOMAT office for our further assistance.
Normally not. Accidental overloads determine maximum forces on the components. Such forces on the base plate are definitely limited, since overload risks are significantly reduced by permitting the blade swing free and clear out of the water. It is therefore sufficient to use conventional or slightly oversized round washers rather than back plate reinforcements on the inside.
Many customers do the installation without professional assistance. After the initial planning and layout with help of 1:10 scale drawings, the actual installation is simple. Only four holes have to be drilled in the hull. The fact that the SAILOMAT uses a universal mounting principle, you are always sure that the unit will be correctly positioned (vertical mast tube). The several options for line circuit layout are described in the SAILOMAT manual, and should be followed closely.
All rights reserved. Patents. Trademark.